Case study / 3D printing in the automotive sector
Production of engine tuning parts – motorsports
See how we improve and produce small batches of engine performance enhancing tuning parts. The process will be similar for parts of any car, bus, truck or even motorbike!
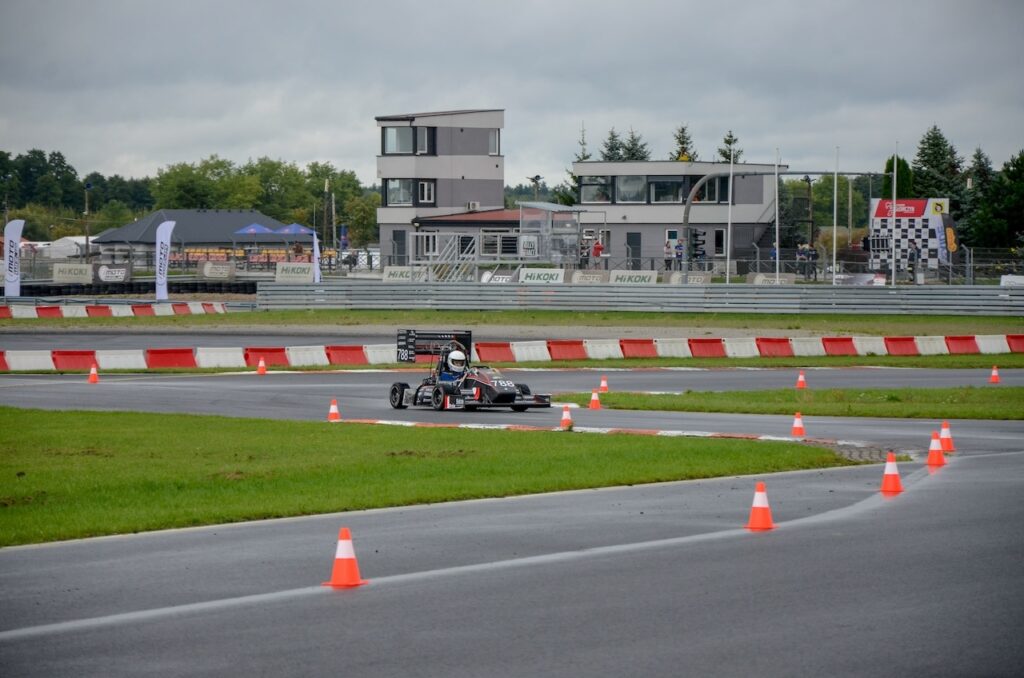
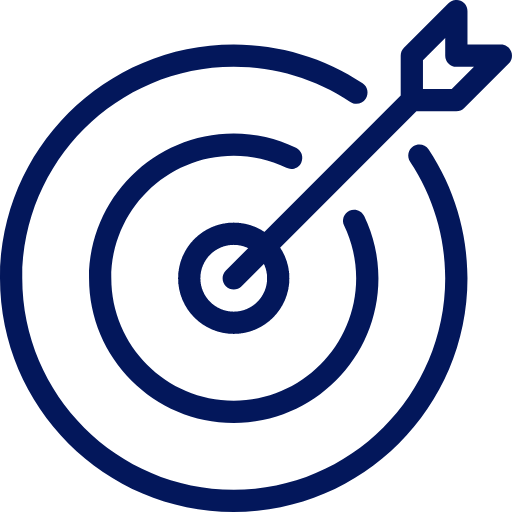
Challenges
- Producing intake system components to enhance the performance of our partner WUT Racing‘s car.
- Maintaining the components’ ability to withstand high temperatures and boost pressure while maintaining tightness.
- Delivering components for testing as quickly as possible.
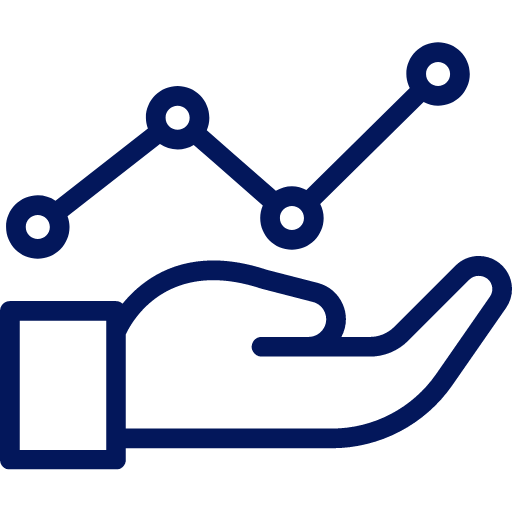
Results
- Reducing the weight of the car while maintaining sufficient performance of the modified components.
- Improved engine performance – increased component roughness reduced air separation in the intake compared to components made of aluminium, for example.
Component I
Intake system venturi
There is a venturi in the intake system – this is a requirement of the Formula Student regulations. This element at its narrowest point can be a maximum of 20 mm if we choose RON98 fuel or 19 mm if we choose E85 ethanol.
The aim of modifying the venturi is to achieve the highest possible airflow with the smallest possible difference in pressure before and after the venturi.
We were able to achieve this by increasing the roughness of the element, which reduced airflow detachments.
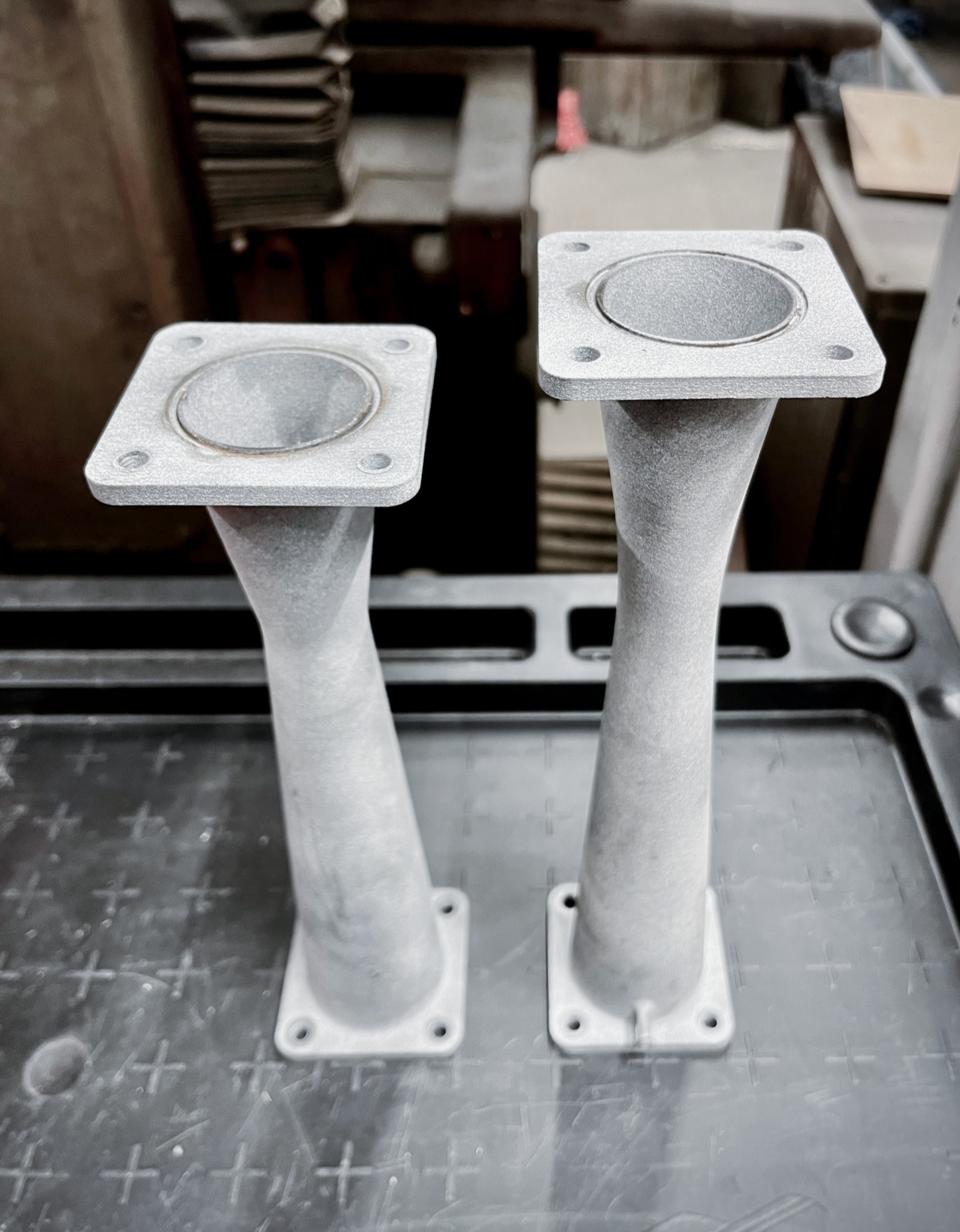
Component II
Throttle valve
We decided to replace the original Bosch throttle housing made of aluminium with a modified housing 3D printed from PA12 material.
The main aim of using the new housing was to reduce weight and we managed to reduce it by as much as 342 g while maintaining the component’s functionality.
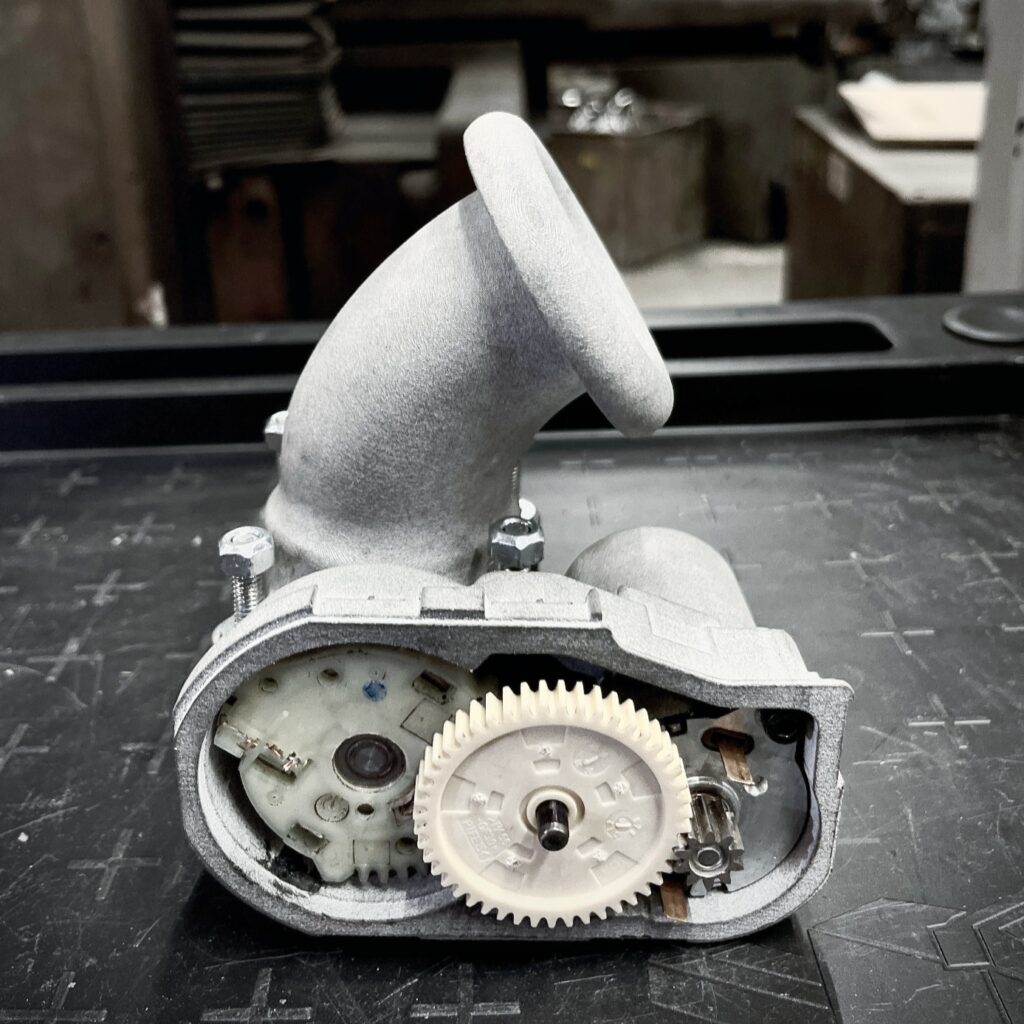
Choice of technology
3D printing with MJF technology
We chose printed components because of the possibilities offered by 3D printing technology.
We reduced the weight and increased the performance of our vehicle. All this, combined with the fast turnaround time, allowed us to start the engine calibration process on the dynamometer sooner.
We chose MJF technology over FDM because of the tightness of the components – the intake system cannot afford leaks. The PA12 material is also resistant to high temperatures.
The venturi in the intake system must be able to withstand the vacuum without deforming. This is the case when the throttle is closed and the engine acts as a vacuum pump and the intake system components deform inwards.
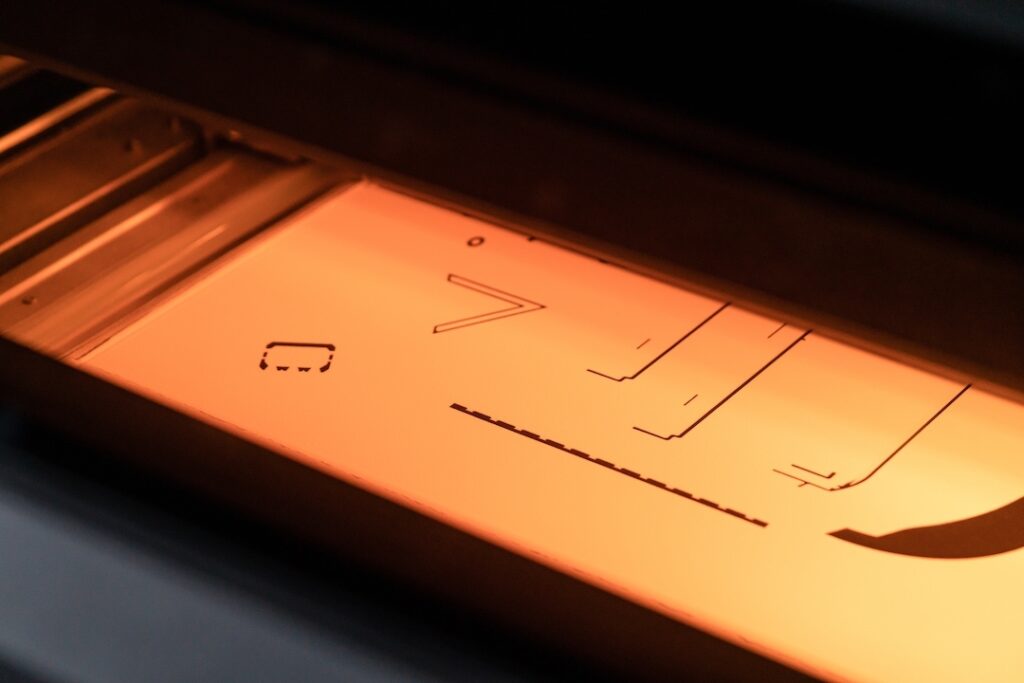
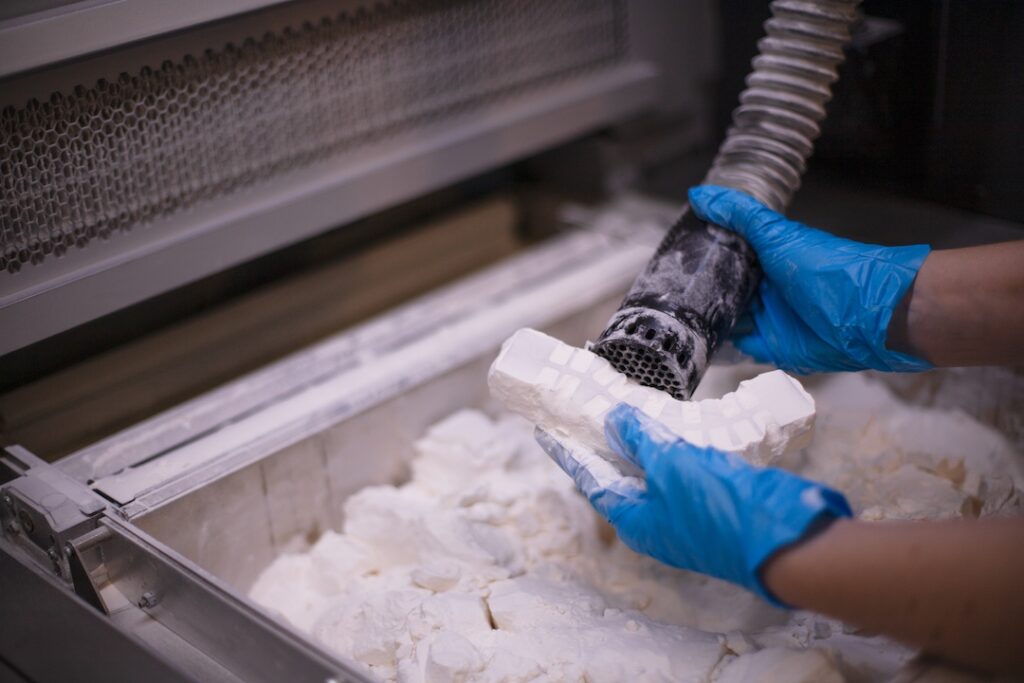
Testimonial
Course of action
We recommend cooperation with Spes3D with a clear conscience. Trouble-free contact – quick and helpful answers in both technical and marketing matters, execution of elements without any reservations and quick deadline. Professionalism can be seen and felt at every stage of cooperation 🙂
Iga Bartosińska
Fundraising Coordinator, WUT Racing
The WUT Racing scientific association was founded in 2011 at the Faculty of Power and Aeronautical Engineering of the Warsaw University of Technology, and has since united motorsport enthusiasts whose aim is to construct and build a racing car suitable for participation in international Formula Student competitions.
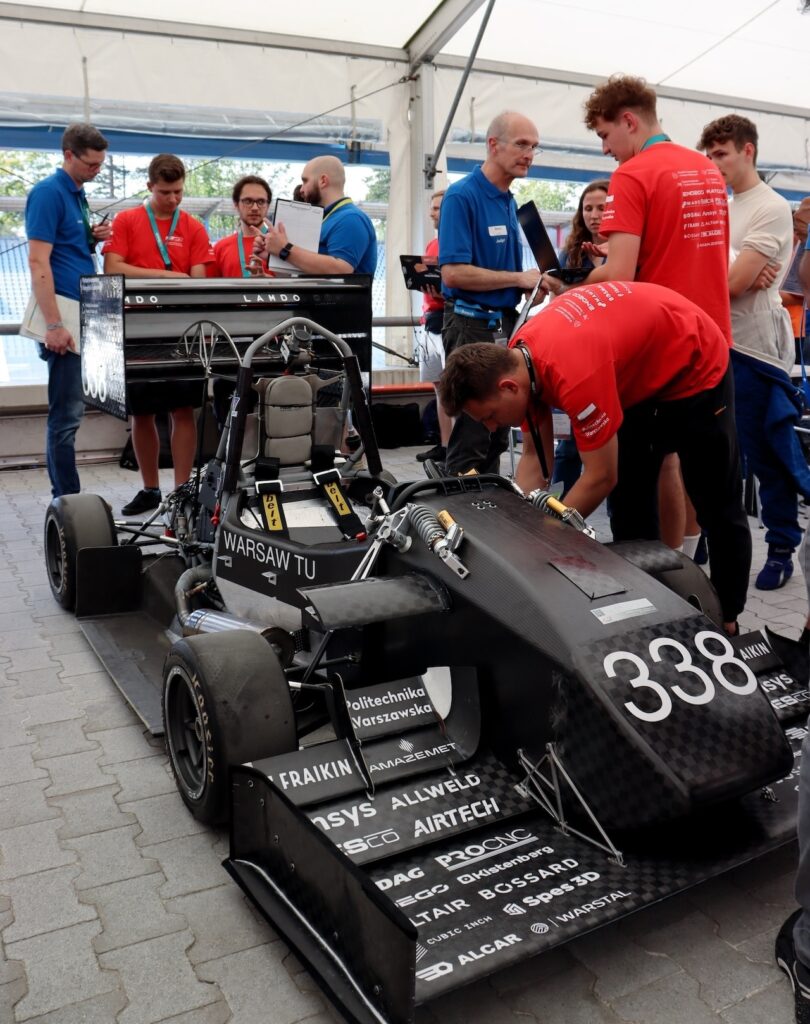
Cooperation
Let’s make it even better. Together!
As a team of experts in the field of incremental technology and machining, we offer a customised approach to our customers’ needs.
Thanks to our knowledge and experience in the automotive and manufacturing sectors, we are able to optimise production processes and provide the best solutions that bring financial, logistical and time benefits to our customers. We act professionally, ensuring fast and timely execution of projects and seamless delivery logistics.
We invite you to work with us to achieve the best results together and increase your competitiveness in the market.
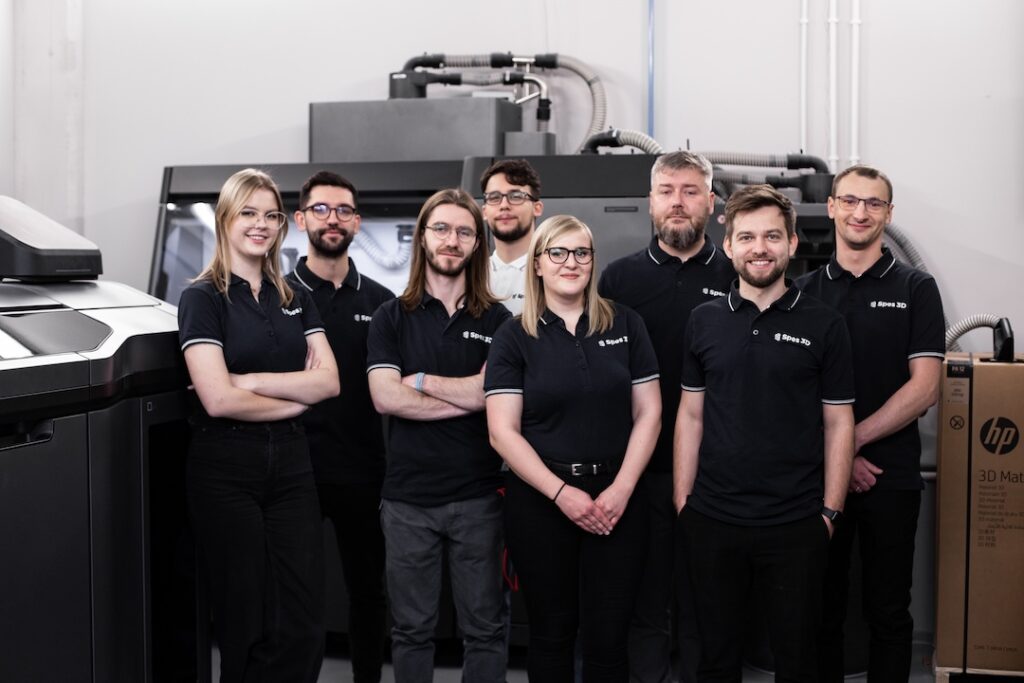