Case study / innovative projects
New generation heat exchangers
Our engineering team took on the challenge of creating a next-generation heat exchanger that is both more compact and more efficient than a standard plate heat exchanger.

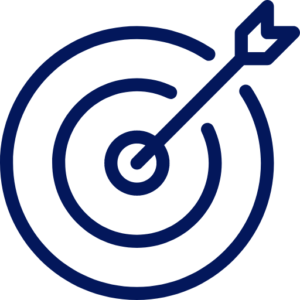
Challenge
Creating a new generation heat exchanger – more compact and efficient than a standard plate heat exchanger.
This is in response to the needs of the automotive and aerospace industries, where these very parameters are crucial.
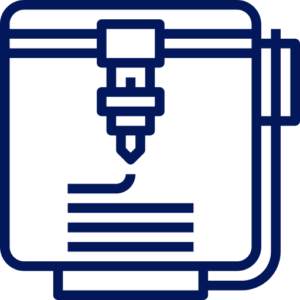
Implementation
Instead of traditional exchanger plates, we used a Triply Periodic Minimal Surface (TPMS) structure.
This unique structure further turbulises the flow, resulting in intensified heat transfer.
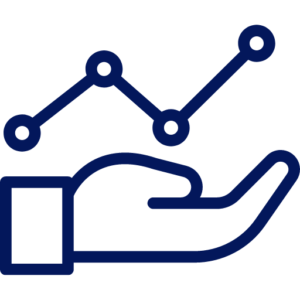
Effects
- Reduction in volume by 27%
- Increase in efficiency relative to a standard heat exchanger by more than 10%.
- Material: 316L stainless steel
- Technology: 3D printing using LPBF technology
Introduction
The role of heat exchangers
The heat exchanger is one of the most important devices in heat management systems.
It is used for energy recovery, temperature control of working fluids, heating, etc.
Heat exchangers are used in the energy, electronics, chemical, aerospace and automotive industries, among others, or as part of HVAC systems for heating, ventilation and air conditioning of buildings.
Start of work
Engineering process
The Spes3D engineering team, led by Krzysztof Kus, took up the challenge and started the process of designing a heat exchanger using a gyroidal TPMS (Triply-Periodic Minimal Surface) structure instead of one of the traditional solutions used in heat exchangers. We began the work by analysing and selecting the appropriate manufacturing technology – LPBF 3D printing in stainless steel.
We carried out a series of computer simulations to select, print and carry out laboratory testing of a prototype of the most promising heat exchanger variant.
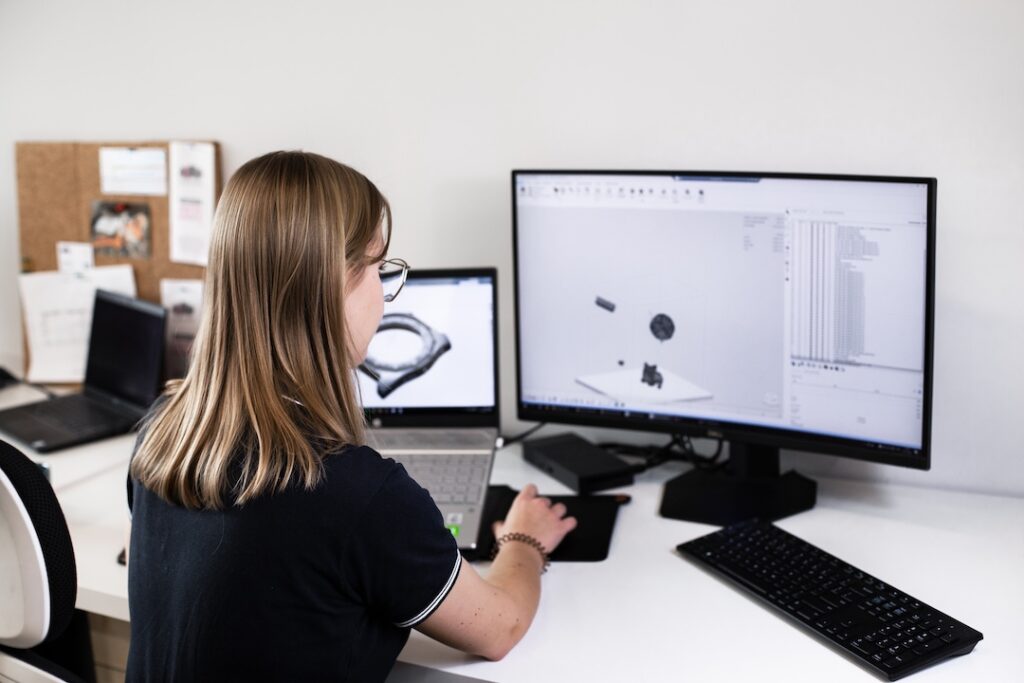
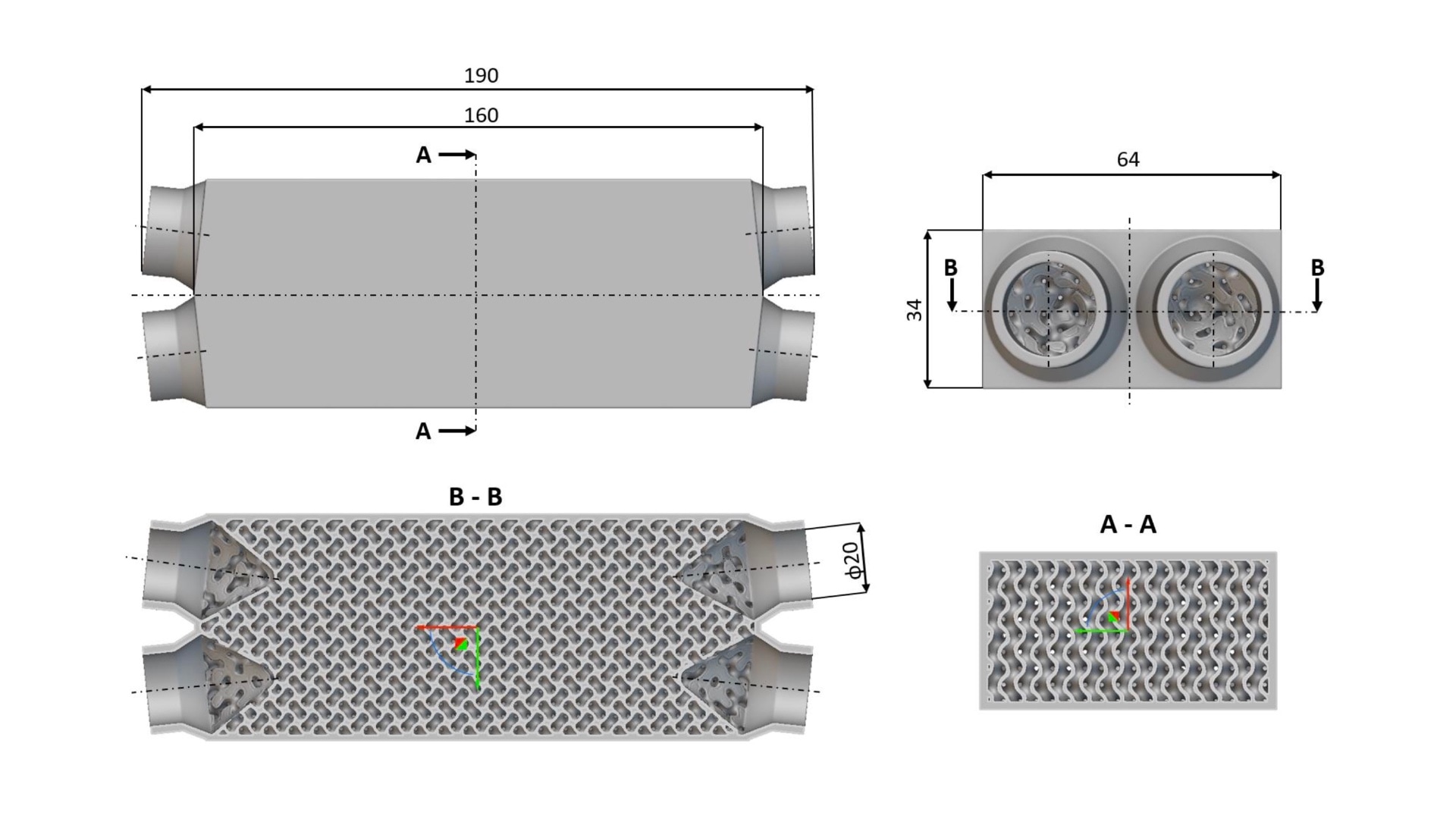
The result of the design work
Visualisation and printed heat exchanger
The new generation heat exchanger developed by Spes3D (blue colour in the visualisation) can be contained in the housing of a classic plate heat exchanger (grey colour in the visualisation , cut in half).
The volume of the Spes3D heat exchanger is 27% smaller than that of a plate heat exchanger with an increased efficiency of more than 10%.
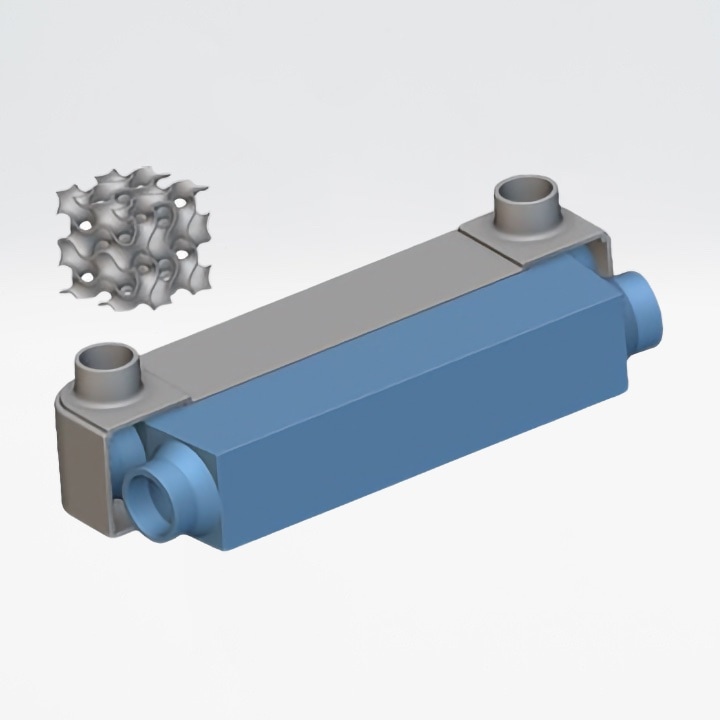
Comparative visualisation

Photo of the Spes3D heat exchanger
Technology
Production capacity
The heat exchanger was 3D printed using LPBF (Laser Powder Bed Fusion) technology in 316L stainless steel. This technology allows components with extremely complex geometries to be printed quickly and precisely.
The printing process for the first prototype took about 24 hours. When production is increased to the simultaneous manufacture of multiple exchangers, the production time for a single exchanger can be reduced to as little as 16 hours.
It is worth noting that the production process is fully automated and does not require the presence of an operator at the machine during the entire time the components are being manufactured, thus significantly reducing production costs.

Result of the work
Achievements, tests and performance
The NTU (number of transfer units) defines “how many units of heat have been transferred” from one fluid to another in relation to the system’s lowest energy.
Despite a 27% reduction in exchanger volume, a 17% reduction in core length and a 15% reduction in heat transfer surface area, we were able to create an exchanger that is more than 10% more efficient than the currently used plate-type solution in terms of heat transfer performance (NTU) and 4% better in terms of overall efficiency.
This shows great potential for the further development of our exchangers, especially once the printing parameters have been mastered to allow a wall thickness of 0.5 mm to be printed.
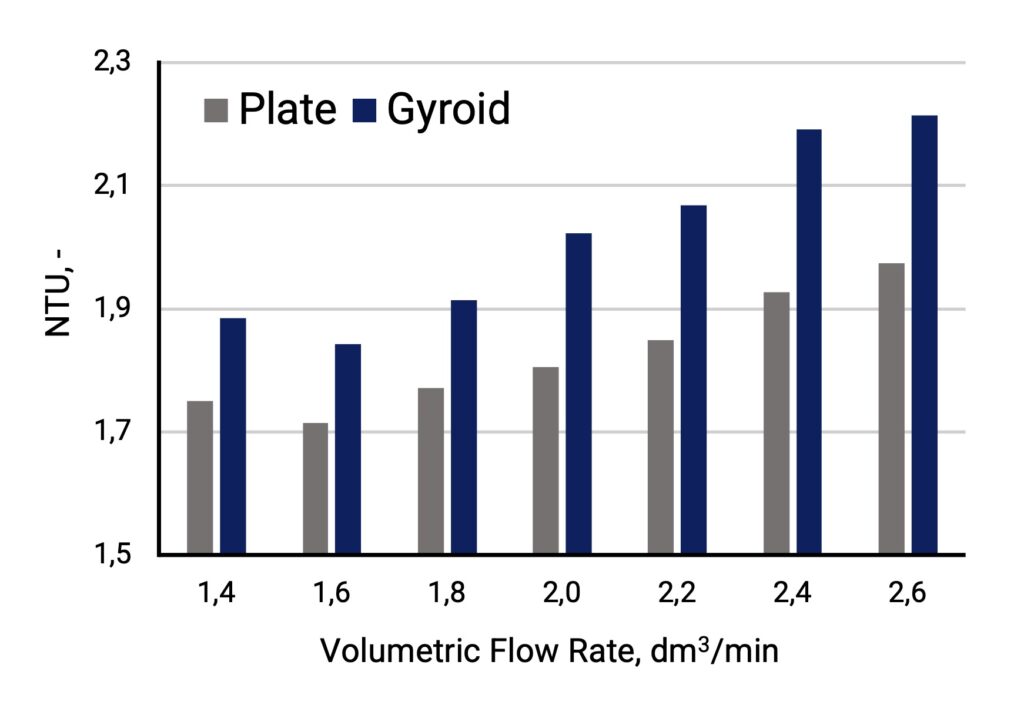
Let’s create something new!
3D printing is our passion, and with the capabilities of one of the most modern machine parks in this part of Europe, we are able to create unique things just for you.
We are a team of experts in design, 3D printing and CNC machining. We will advise improvements. We will select the technology. We will prepare prototypes.
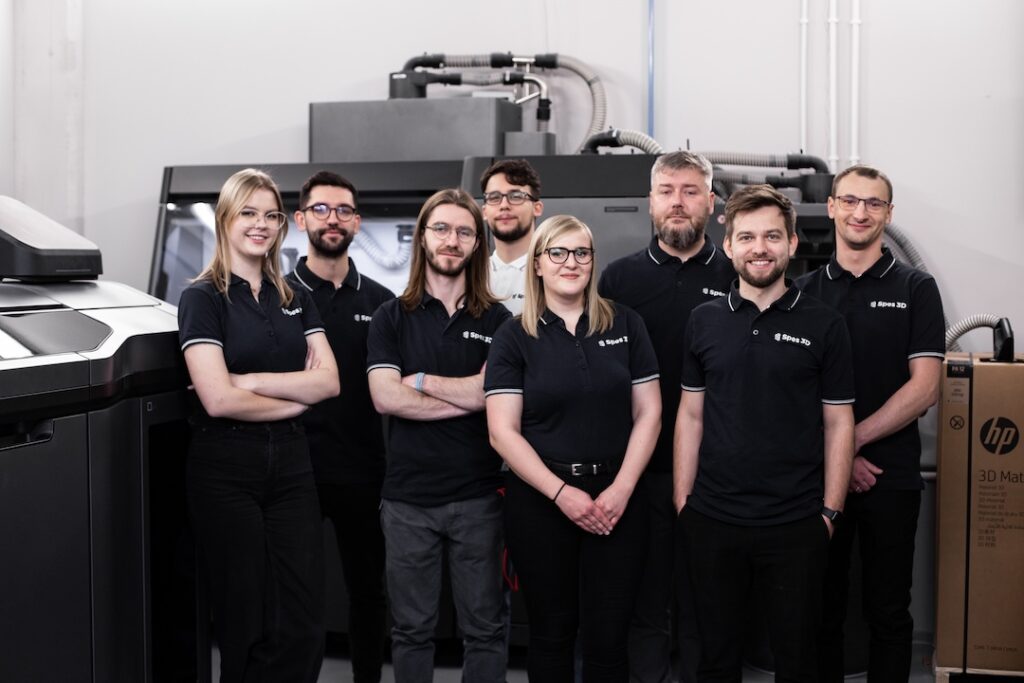