Case study / 3D PRINTING IN THE AUTOMOTIVE SECTOR
Gauge optimisation
A company in the automotive sector commissioned us to optimise the design and manufacturing process of a gauge used to check the geometry of the polymer lines being manufactured.
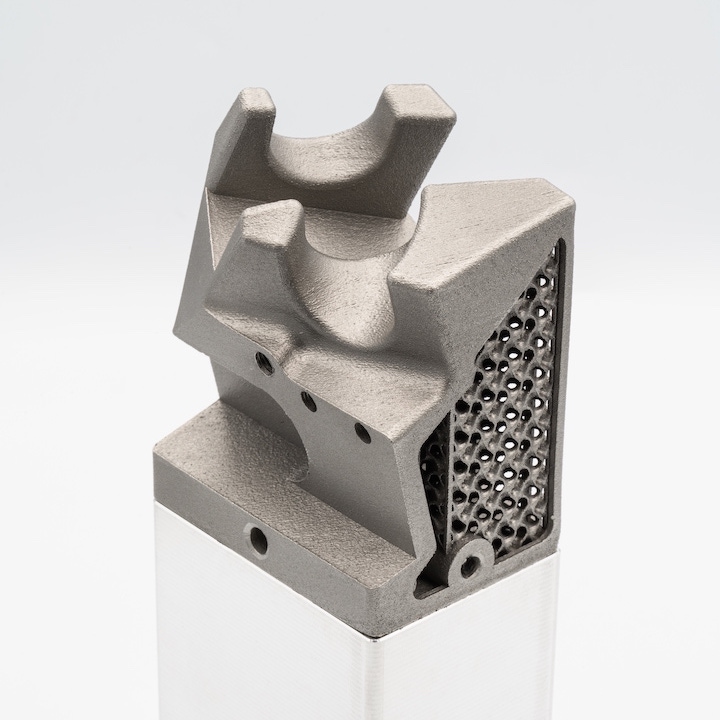
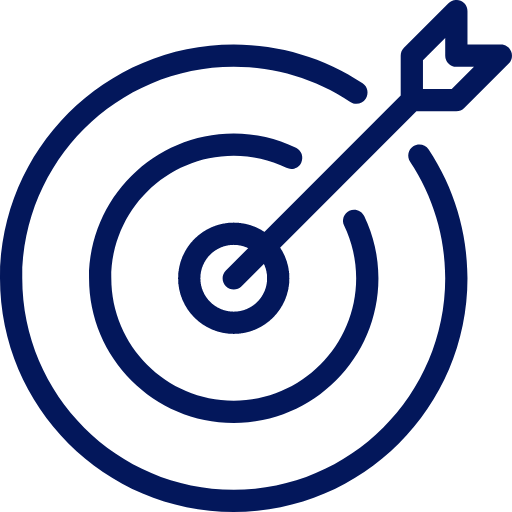
Challenges
- Increasing the robustness of a component
- Reducing waiting times for parts
- Reducing production costs
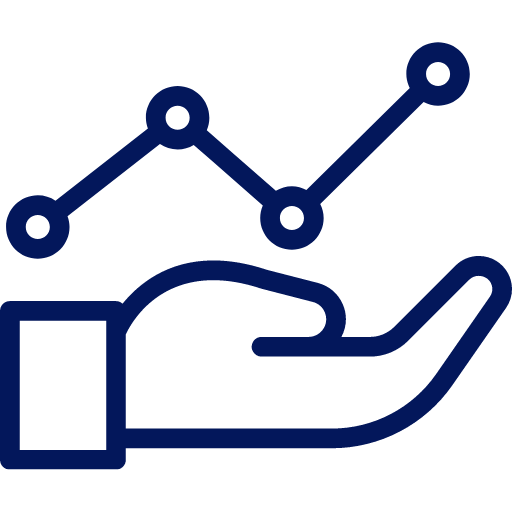
Results
- Increased strength – aluminium replaced by stainless steel
- Reduced weight by 9%
- Reduction in waiting time from 5 weeks to 5 days
- Cost reduction of 30%

Technologies
- 3D printing in stainless steel using LPBF technology
- Aluminium machining (CNC)
- Post-processing
INTRODUCTION
Geometric gauges in the automotive industry
In the automotive industry, some of the most critical components at the production stage are so-called gauges, or geometric gauges. These components are essential for checking the correctness of manufactured mechanical, electrical and electronic systems in passenger cars.
They can be time-consuming and costly to produce using traditional methods. Due to their low volume and complex geometry, their production often requires five-axis CNC machines.
Through the use of modern manufacturing technologies, such as incremental manufacturing (3D printing), the production of gauges can be significantly streamlined.
In this case study, we will present an example of optimising the production of a gauge for fuel system hoses for passenger cars, where we applied modern manufacturing technologies to achieve tangible results and benefits for our customer.
Preparations
Engineering process
The Spes3D engineering team took on the challenge and started the gauge design process. We started the work by analysing and selecting the appropriate manufacturing technologies – 3D printing from stainless steel using LPBF technology and cutting aluminium on a simple 3-axis CNC machine. We then tackled the optimisation of the 3D model of the tool, where we focused on exploiting the possibilities offered by 3D printing – the ease of producing complex geometries, the speed of making low-volume and personalised parts without the need to retool the machine.
By leveraging these features, we achieved a number of benefits for our client.
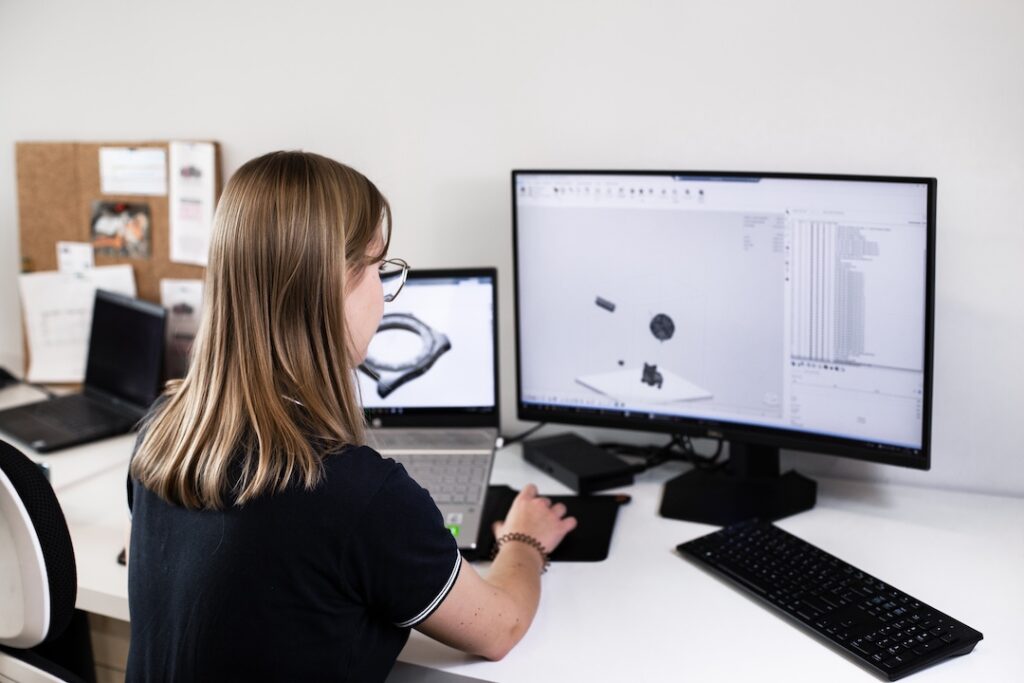
SOLUTION I
Splitting the gauge into two parts
In order to reduce production costs and shorten the manufacturing time of the gauge, it was decided to divide the gauge into 2 parts: the lower part of the gauge was intended to be made of aluminium on the milling machine due to its low complexity, and the upper part was intended for 3D printing in stainless steel.
Both parts were remodelled in such a way that they could be joined easily, quickly and, above all, precisely.
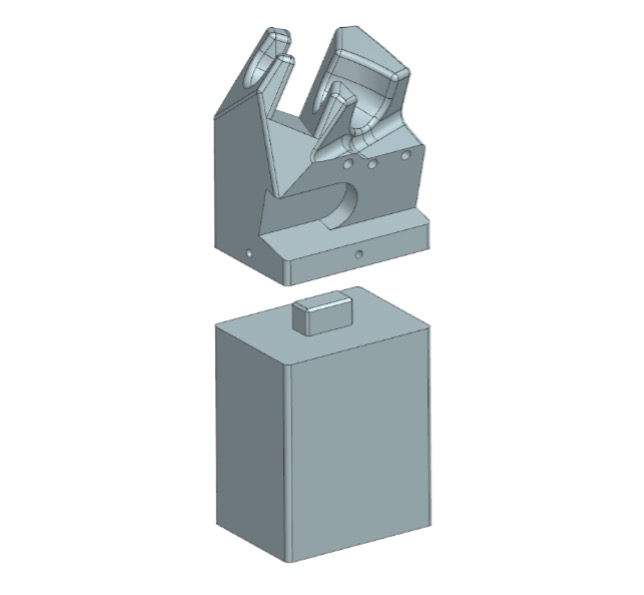
SOLUTION II
Optimising the design of the upper section of the gauge
Using CAD software, engineers optimised the geometry of the upper part of the gauge in such a way as to reduce its volume and, therefore, the weight and amount of material used in production. An additional resultant of the volume optimisation will be a reduction in the part’s manufacturing time in the incremental manufacturing process.

With the help of NX software and Materialise Magics, material was removed from areas where it was not needed and lattice (gyroid) support structures were inserted where necessary to make the part LPBF feasible, while maintaining sufficient stiffness and strength of the part.
This reduced the volume of the gauge top from the original 137.7 cm3 to 43.2 cm3, resulting in a weight reduction from 371.8 g (for the solid aluminium top) to 336.9 g (for the optimised steel top).
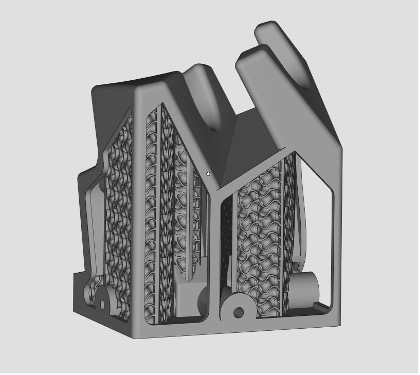
TECHNOLOGY
3D printing using LPBF technology
The upper part of the gauge was printed using LPBF (Laser Powder Bed Fusion) technology in 316L stainless steel. This technology allows parts with complex geometries to be printed quickly and precisely. The printing process for one upper part of the gauge took approximately 14 hours. When production was increased to printing 20 parts at the same time, the production time was about 76 hours, which is less than four hours per part.
It is worth noting that the production process is fully automated and does not require the presence of an operator at the machine for the entire time the parts are being produced, allowing for a significant reduction in production costs.

Post-processing
Machining and joining the parts
Once the part was printed, the post-processing process, i.e. the surface treatment, began. Two different abrasive media, electro-corundum and micro glass beads, were used to achieve the right surface quality and remove any imperfections.
The bottom surface of the printed part, which is the contact surface between the upper and lower parts of the gauge, was then spliced on a milling machine to allow the parts to be perfectly joined.
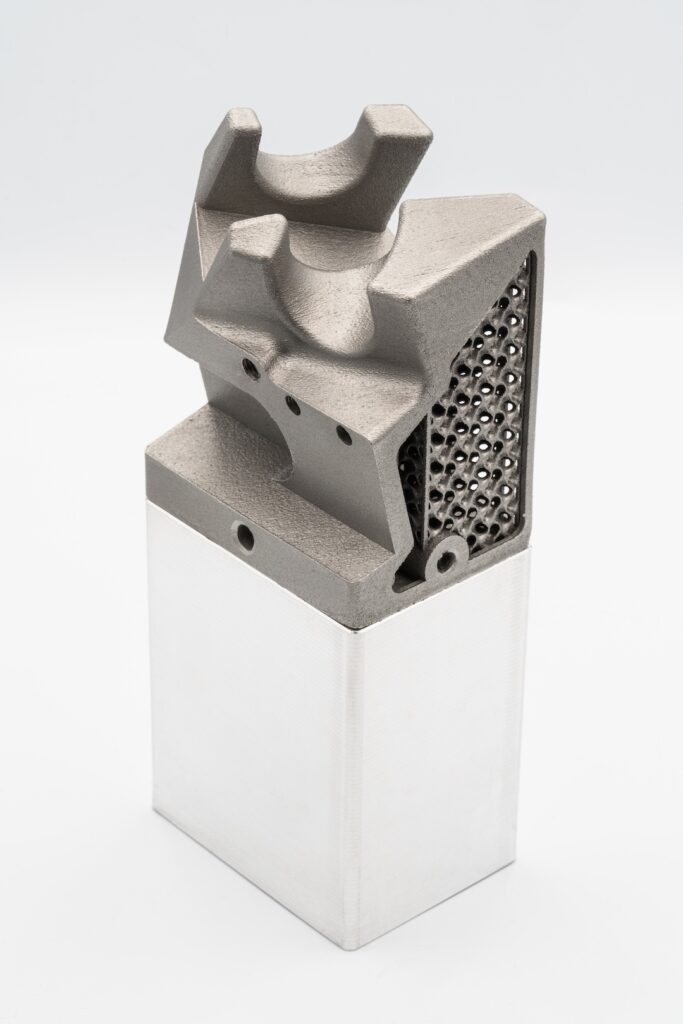
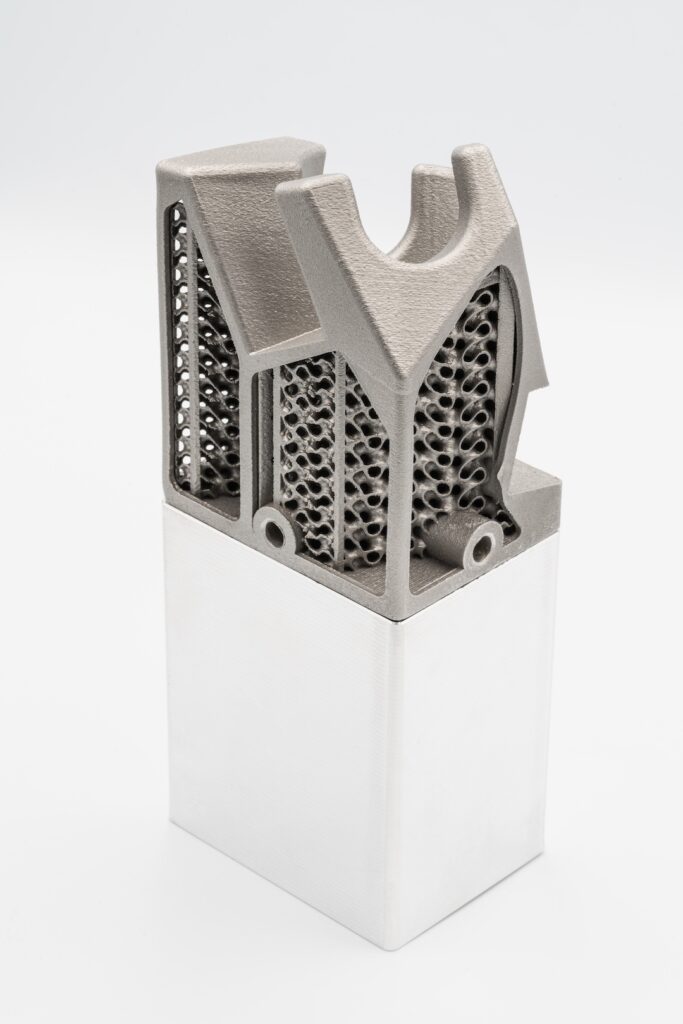
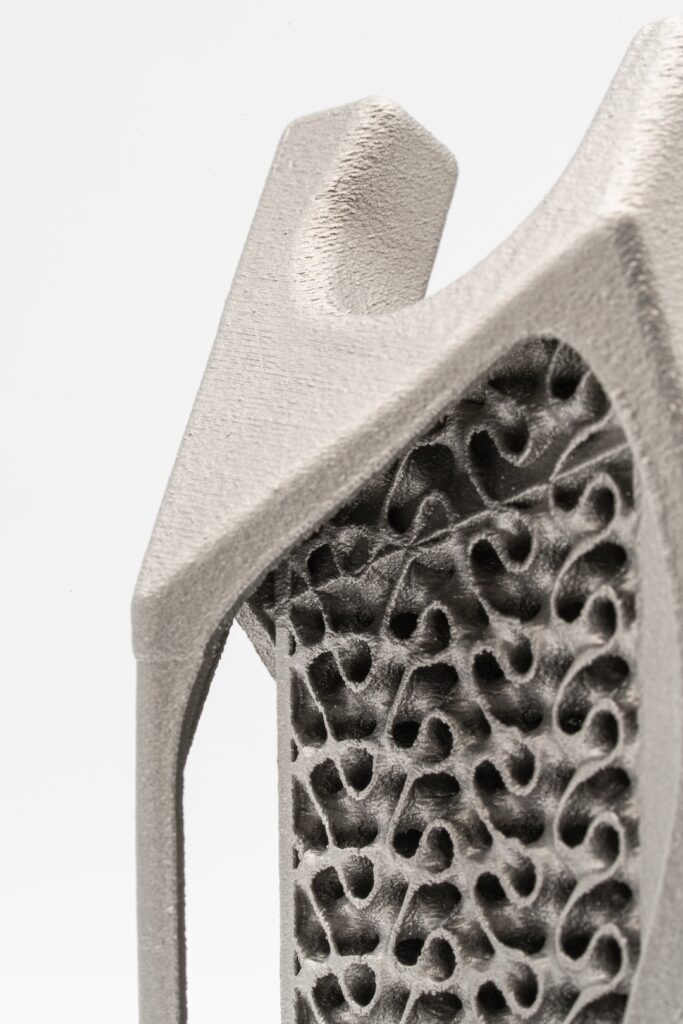
OUTCOME OF THE WORK
Quality control
The final stage of the process was to carry out quality control, i.e. to compare the printed part with the 3D model to confirm the geometric conformity with the design. To do this, a 3D scan of the manufactured solution was made. The scan was then compared with the model and the deviations on the working surfaces of the gauge were determined.
According to the customer’s requirements, these did not exceed 0.1 mm.
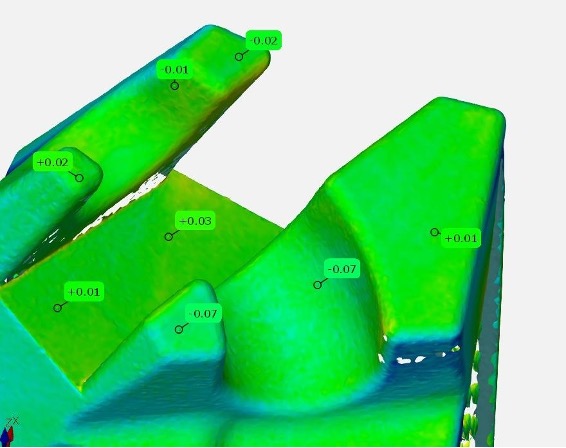
SUMMARY
Results achieved
By optimising the design of the gauge top and manufacturing using 3D printing technology in combination with traditional material cutting, it was possible to achieve significant benefits for the end customer of the manufactured gauge.
In addition, Spes3D defined the possibility of further optimising the solution by bonding other components that are currently attached to the printed gauge to the printed gauge, thus further reducing the costs associated with the assembly of the gauge components.
- Increased strength and therefore service life of the gauge by making the working part of the gauge from a harder alloy – stainless steel instead of aluminium.
- Reduction in gauge weight by 9%.
- Reduction in total production time for 20 gauges from 5 weeks to 5 working days (3 days for printing and 2 days for post-processing and assembly).
- Reduction in component manufacturing costs by 30%.
COOPERATION
Let’s make it even better!
As a team of experts in the field of incremental technology and machining, we offer a customised approach to our customers’ needs.
Thanks to our knowledge and experience in the automotive and manufacturing sectors, we are able to optimise production processes and provide the best solutions that bring financial, logistical and time benefits to our customers. We act professionally, ensuring fast and timely execution of projects and seamless delivery logistics.
We invite you to work with us to achieve the best results together and increase your competitiveness in the market.
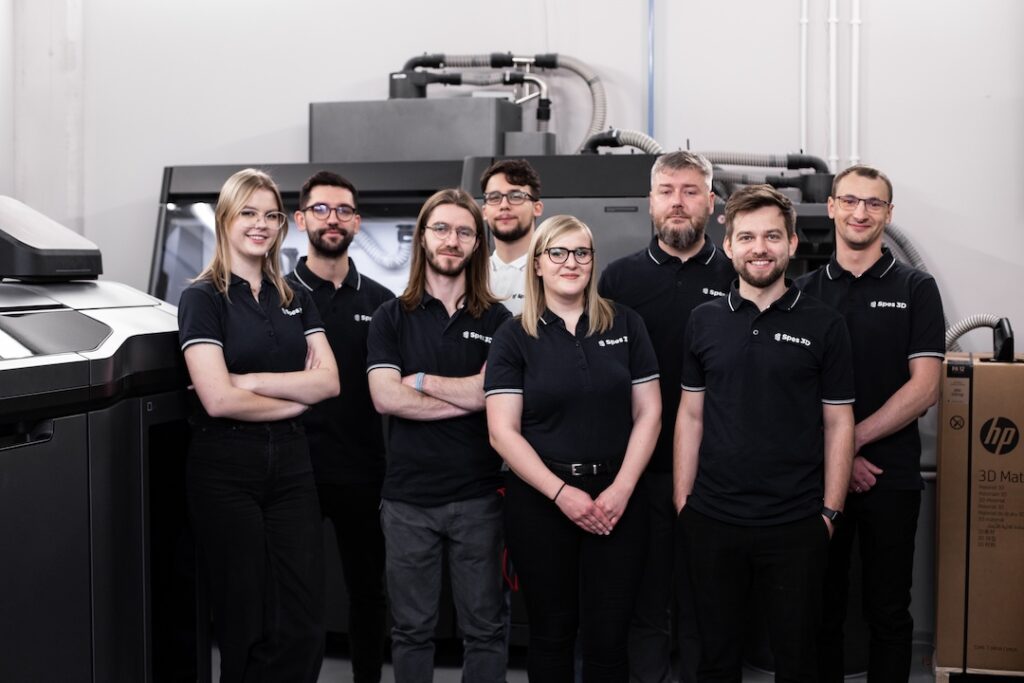